Заводи Росії. Як роблять шини Nokian
Коли 11 років тому в Nokian Tyres було прийнято рішення відкрити завод в Росії, ніхто не припускав, до чого це призведе. Фінська компанія на той момент існувала вже 106 років, і її співробітники знали про шини і їх виробництві все. Але практика показала, що їм доступні не всі секрети цієї справи, і вони можуть помилятися.
Завод Nokian Tyres Russia
Завод розташований за адресою: Ленінградська область, Всеволожськ, промзона «Цегельний завод», квартал 6.
Запуск виробництва: сентябрь 2005 р
Кількість працівників 1300.
Виробнича потужність заводу: 15 500 000 шин на рік.
Розмір інвестицій: € 800 000 000.
Будівництво заводу у Всеволожську почалося в 2004 році після двох років узгоджень і тверджень бізнес-плану. Першим в 2005-му заробив цех з виробництва компонентів і складання шин, але екскурсія стартує в іншому місці - цеху міксинг, або резіносмешенія. Саме з процесу виробництва гуми і починається створення шини.
Перед нами ліс труб, своєю висотою і різними діаметрами нагадують реліктові дерева. Найбільші цистерни, висотою 30 метрів і 4 м в діаметрі, які вміщують 360 кубометрів сировини, навіть не помістилися в цеху, вони прибудовані до нього зовні. У них міксується суміш з сажі (технічного вуглецю) і каучуку, а всередині на різних рівнях п'ятиповерхової будівлі додаються силика, сірка, масла і інші хімічні складові, що визначають властивості кінцевої суміші. Вся маса повільно проходить шлях від низу до верху і зверху вниз і повертається на нижній рівень у вигляді стрічок товщиною 2-3 сантиметри і шириною 60-70 см. Разом зі спуском суміші знижується і її температура - з максимальних 170˚С, при яких перемішування йде швидше за все, до 100 ˚ С після додавання сірки. За словами директора з виробництва Nokian Tyres, а в цей раз і мого екскурсовода, Олександра Уставщікова - весь завод працює на те, щоб температура не піднялася вище тих самих 100?, Щоб передчасно не почався процес вулканізації.
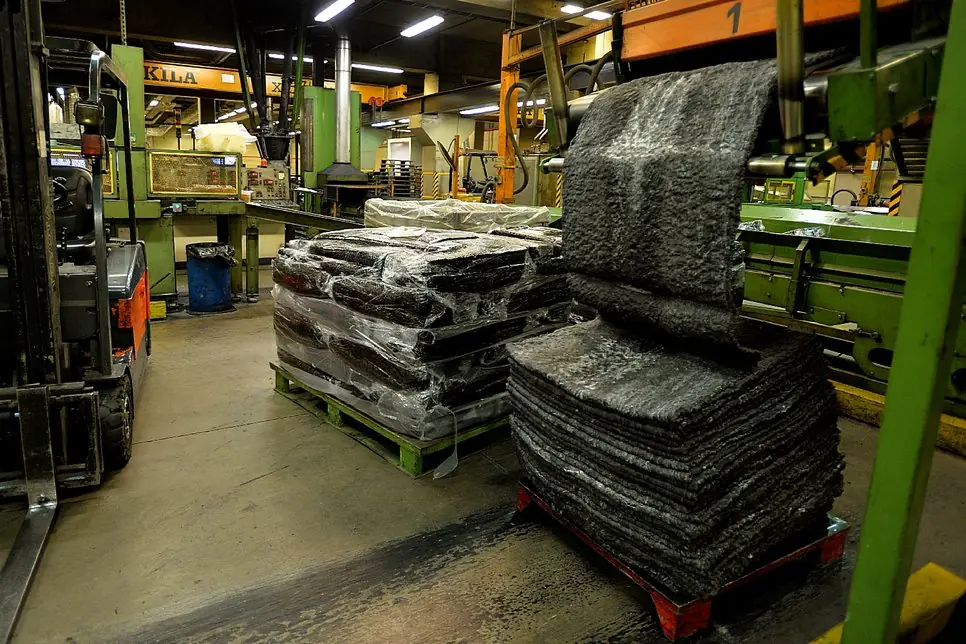
На самому першому плані видно результат початковій стадії обробки каучуку - мастіс, в який пізніше додадуть сажу і вийде гума. За ним в поліетилені основну сировину - натуральний каучук, який привозять під Пітер з Малайзії, В'єтнаму, Індонезії та інших країн. За ним видно світлий брусок на конвеєрі - це найчистіший каучук, максимально очищений від природних домішок. Його додають при створенні зимових шин, а синтетичний каучук (майже прозорий) входить до складу суміші для літніх
Дивно, але в цьому величезному приміщенні ми зустріли тільки одну людину, який готував натуральну сировину для подачі в гігантський міксер. Ще один - оператор цеху, знаходиться в окремому приміщенні рівнем вище і стежить за роботою за показаннями всіляких датчиків, дані від яких зводяться в єдиний командний пункт. Втім, малолюдно, як з'ясувалося пізніше, це характеристика всього підприємства. У цехах в одну зміну одночасно працюють 250 чоловік, а загальна чисельність працівників заводу - від генерального директора до кухаря в їдальні - близько 1300.
При повному завантаженні цех міксинг може виготовляти 400 тонн гумових сумішей на добу. Можна було б заважати і більше, якби на всю шину йшла одна-єдина суміш. Але їх потрібно мінімум вісім. Варіацій додає облік сезонності, класу автомобіля, призначення шини. В результаті набирається близько 30 різних сумішей, які мікс на 12 лініях. І з цього моменту починається магія цифр, що зробила завод Nokian Tyres одним з найбільших підприємств в світі і першим в Росії з випуску шин.
Завод може випускати 1700 продуктів в рік і 120 в день, і кожен день 10 з них змінюються. Тут не можна плутати продукт і модель, тому що в рамках останньої може бути кілька типорозмірів. Конкретна шина в конкретному розмірі - це і є продукт. Для того, щоб почати випуск нового продукту, потрібно від 3 до 20 годин. Найбільше часу зажадає створення нової суміші. А поки вона буде «варитися», поміняють програми і обладнання на лініях випуску компонентів і пресів. У останніх потрібно знизити температуру, потім замінити блоки з малюнком і знову набрати робочу температуру. Мінімальна партія становить всього 100 шин, чим пояснюється пропозицію одного з найбільших асортиментів типорозмірів
Завод щорічно може випускати 15,5 мільйона шин. По першому бізнес-плану максимальна потужність підприємства становила 4 мільйони - тоді гумові суміші привозили з Фінляндії. З 2006 року з появою цеху міксинг і після запуску додаткових ліній продуктивність піднялася до 8 мільйонів. Зараз же шини збирають 13 ліній, і готується 14-я, з якої продуктивність заводу зросте до 17 мільйонів. Рекорд був поставлений 8 вересня 2013, коли за добу випустили 45 513 шин. Він був би давно побитий, якби не економічна ситуація в країні зі зниженим попитом.
Але завод не бідує, навіть незважаючи на те, що закуповує частину сировини за валюту. По-перше, це все-таки частина, а деякі складові суміші все ж роблять в Росії. Наприклад, «Сибур» поставляє синтетичний каучук. По-друге, за даними «Автостат» на кінець 2015 року, Nokian воліють 47% автовласників, спад є, але продажу-то йдуть. І третє, але не останнє: Всеволожский завод експортує (а значить, отримує тверду валюту) близько 70% всього обсягу в більш ніж 40 країн світу, в першу чергу Центральну Європу і Північну Америку. Німці і американці, напевно, сильно дивуються, коли бачать на етикетці напис «Made in Russia».
Гума - це, може бути, зараз один з найбільш натуральних продуктів, навіть у порівнянні з тим, що ми їмо. Каучук, що міститься в соку дерева гевея, поки замінити нічим. Хіміки вже придумали, як штучно створювати довгі молекули з вуглецевої основою, але не знають, як закріпити зв'язку між ними, для створення еластичності рівня натурального каучуку.
З гарячого цеху резіносмешенія ми переходимо на його невеликий склад. Стопки гумових стрічок були б жахливо нудними, якби не три речі. Перша - шість роботів-навантажувачів, які в автоматичному режимі розподіляють гумові суміші по стелажах і перевозять в цех виготовлення компонентів. Щоб вони орієнтувалися в просторі, на стінах повісили дзеркала, а для швидкого зчитування інформації на полицях і на стопках приклеєні ярлики зі штрих-кодом. Щось зачаровує і лякає є в роботі цих тихих трудівників - починаєш думати, що у машин є розум. Заспокоює лише те, що у них сідають акумулятори, і змінює їх людина.
Друга примітна річ - самі стрічки, а вірніше, що виступають шари з обрізаними кутами. Їх зазвичай по 4-5 на кожній палеті, і поділяють вони між собою близько 200 кг гуми, які на заводі називають патчами. Обрізані кути потрібні для перевірки якості приготовленої суміші, а стрічці вони ніяк не шкодять, оскільки перед створенням того чи іншого компонента гума знову розм'якшується нагріванням і перемішується.
І третє - це система передачі цих зрізаних куточків в лабораторію. Для того, щоб це відбувалося швидко і без плутанини, з цеху міксинг проходять труби пневмопошти. У колбах по ним передають зразки для тестів, а у відповідь реакцією стають наклейки з принтера - білі, якщо все в порядку, і червоні, якщо з сумішшю щось не так.
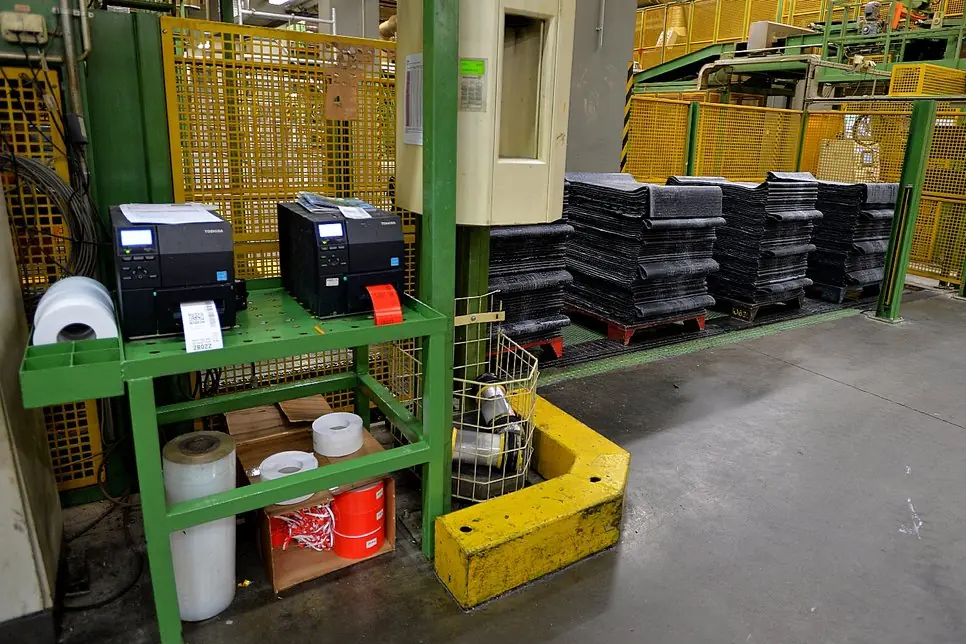
У центрі фотографії - ящик для відправки пневмопошти, поруч з ним принтери, що видають вердикт, а справа «підсудні» - стопки свежеприготовленной гуми, яка чекає схвалення
Всього за добу лабораторія може перевірити близько 2000 зразків гумової суміші, до яких додаються тести сировини і глибокий аналіз того, що робити з гумою, що отримала червону етикетку (таке трапляється нечасто). Перевірка йде за кількома параметрами - хімічний аналіз суміші, потім - механічні випробування на еластичність вулканізованої на мікропрессах гумі. Для цього з відрізаних куточків робляться таблетки, кожна з яких піддається окремому тесту. Більшість з них відбуваються в автоматичному режимі, а еластичність перевіряють вручну: з тестового зразка вирізують детальки, схожі на витягнуті пісочний годинник, їх широкі частини затискають, і машинка починає розтягувати їх. Все розтягування закінчуються розривом, що супроводжується бавовною, але для вимірювань важливо, коли він стався - якщо раніше або пізніше визначеного часу, значить, суміш неправильна.
Є в лабораторії і досить складні прилади, які в основному використовуються для визначення якості вхідної сировини: абсорбціометр вимірює здатність технічного вуглецю поглинати масло, спектрометр визначає присутність і кількість окремих хімічних елементів, колориметр тестує реакцію речовин на температуру. Для перевірки проблемної суміші і розуміння, що ж з нею не так, використовують термогравіметричний метод. Через відрізняються молекулярних мас різні продукти згорають при різній температурі, що і дозволяє визначити точне співвідношення елементів.
Слідуючи за роботами-навантажувачами, ми переходимо в цех компонентів. Зміну обстановки найпростіше визначити за звуком: замість мірного бурчання при перетравленні десятків тонн гуми приміщення наповнене гулом, дзижчанням і потріскування сотні різних механізмів, що виконують зовсім різні функції, але заснованих на обертанні, повільному або швидкому. У цьому цеху виготовляються компоненти. По суті, це створення окремих шарів шини, кожен з яких виконує ту чи іншу обов'язок: протектор забезпечує зчеплення, гермослой тримає повітря, щільні кільця притискають шину до диску, шари з текстильним і металевим кордами забезпечують форму і перешкоджають пошкоджень.
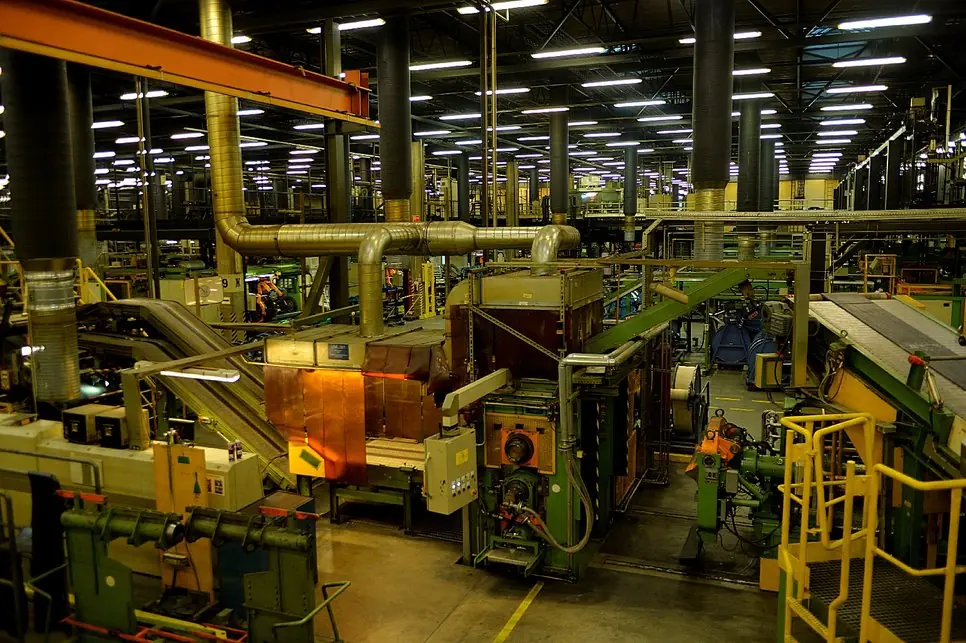
Машина для створення протектора нагадує собою м'ясорубку, але тільки довжиною 20 метрів і з набагато більш складною структурою, яка наводить на думки про нескінченні сходах Ешера. Таких на заводі сім
У гігантську воронку завантажується розігріта гума, причому таких входів чотири - для різних типів сумішей
В черговий раз все перемішується і рухається по лабіринтах труб і конвеєрних стрічок, щоб в кінці вийти у вигляді декількох тонких смуг. Таке паралельне існування короткочасно - вони збираються по верствам в єдину стрічку і проходять через спеціальну насадку, яка формує той чи інший вид профілю протектора
Гермослой - найтонший і еластичний з компонентів шини. У ньому найбільше чистого натурального каучуку, і тому він схожий на латекс. Надлишки, зрізані з боків, тут же подаються на нагрів і заміс і використовуються для створення нової стрічки
Текстильний корд робиться все в двох варіантах, тому відразу обрезінівают цілі полотна. Нейлон обволікається чорної масою і проходить між декількома валами, поки товщина не досягне значення 1,27 мм і менше. Перестаратися з утоньшение теж не можна - мінімальний шар гуми і тканини повинен бути в 0,6 мм. Товщина шару, як і у інших компонентів, перевіряється ультразвуком. Ближче до кінця операції на поверхню текстильного корду накладають тонкі нитки, вони знадобляться при вулканізації: по волокнам буде виходити повітря, який міг потрапити між шарами в процесі складання. Його там бути не повинно, адже бульбашка - це потенційна грижа
Готові компоненти в котушках чекають своєї черги на збірку
Коли виготовлені всі необхідні компоненти, шину можна збирати. Це відбувається на 46 машинах в автоматичному режимі. Спочатку йде гермослой, зістиковано з боковинами, потім накладається текстильний корд (для шин великого діаметра його кладуть в два шари), далі сталевий корд і стрічка GLB, що закриває шов, і завершує все протектор. Оператору потрібно підігнати котушки з цими компонентами до приймачів, заправити в них стрічки і задати комп'ютеру програму збірки. Довжину стрічки, черговість шарів і операцій техніка визначає сама. На машинах, встановлених під час запуску першої лінії, потрібна людина, щоб надіти бортові кільця. Він же є і контролером якості «зеленої» шини - так називають склеєну форму, готову до вулканізації.
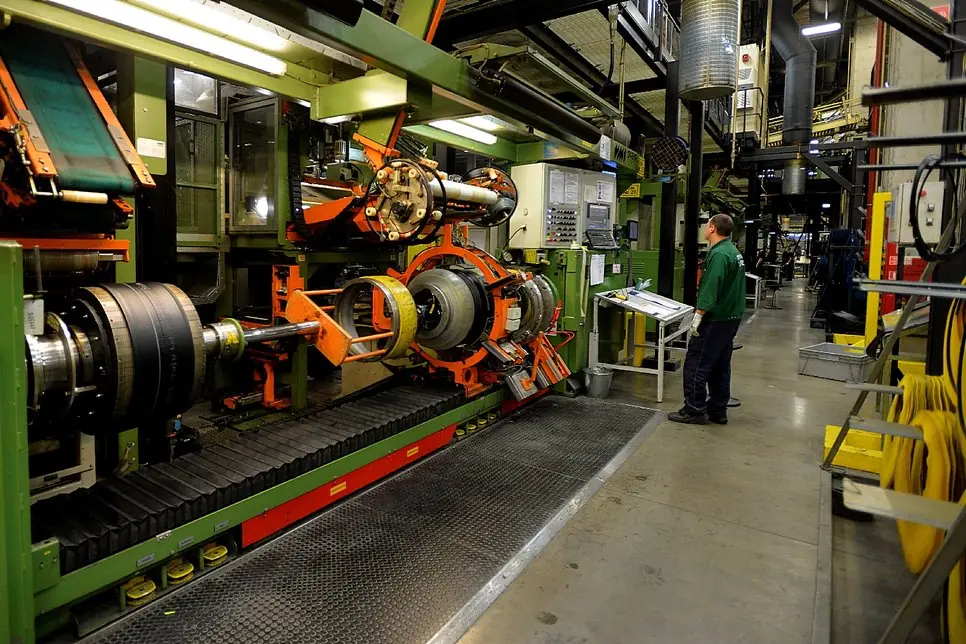
Напівпрозорий міхур пневматичної діафрагми надувається, щоб скласти боковини навколо бортових кілець, виходить нерозривний конструкція. До речі, діафрагми також виробляються на цьому заводі
Повністю в автоматичному режимі працюють машини VMI MAXX 20. Перший промисловий агрегат голландської компанії VMI - лідера з постачання обладнання для шинних заводів, був встановлений саме на Всеволозькому заводі «Нокіа». Причому спочатку прототип обкатали на виробництві в Фінляндії, і вже після внесених до нього змін, необхідних для запуску промислового складання, почалися поставки. Ще не були встановлені всі машини, за контрактом голландці не мали права продавати їх іншим шинникам. VMI MAXX 20 на 50% ефективніше машин попереднього покоління за рахунок того, що частина процесів йде не послідовно, а паралельно. Завдяки цьому потенційний обсяг випуску заводом зріс з 11 до 17 мільйонів шин на рік.
Наступний етап - вулканізація. «Зелену» шину поміщають на спеціальне «ложе», звідки вона переноситься в прес. Усередині нього паром нагнітається необхідний тиск в 15 атмосфер, щоб склеїлися всі верстви, а гума проникла в усі куточки форми і вийшов той малюнок протектора, який закладений розробниками. Пар ж прогріває шину до температури в 170-180˚C, при якій каучук вступає в необоротну хімічну реакцію з сіркою та іншими елементами. На «пропікання» однієї шини йде від 9 до 12 хвилин, в залежності від її розміру.
Час і температура вулканізації також закладені в програму і визначаються автоматично. Для того щоб гума не «пригоріла» і не залишилася сирої, ці параметри підбираються вкрай ретельно в фінському центрі розробки, а на заводі їх потрібно лише дотримуватися
Неспішне пересування шин після вулканізації забезпечується невеликим нахилом пандуса. Поспішати ж нікуди - гума повинна охолонути
Готові шини проходять цілий набір різноманітних перевірок, причому на початковому етапі всі тести роблять роботи, і в самому кінці - люди. Вони краще машин знаходять проблемні місця і ставлять свій особистий штамп на перевірений продукт. Інспекторами за якістю найчастіше стають найкращі оператори складальних агрегатів або вулканізатори.
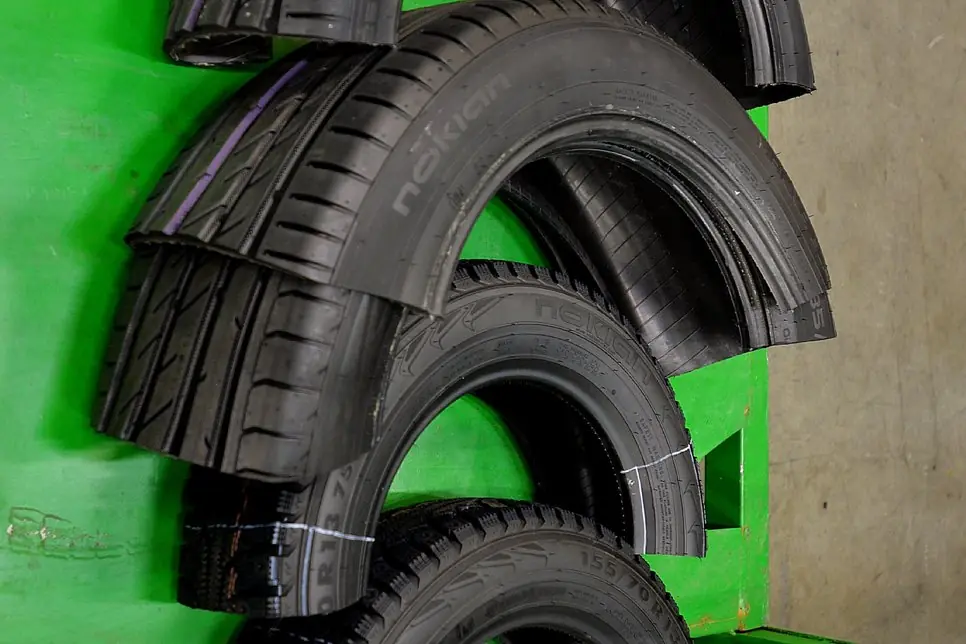
Забраковані по якомусь параметру шини розрізаються на половинки - це самий гарантований спосіб випускати на ринок тільки якісну продукцію
Коридор пов'язує виробництво зі складом, на який шини надходять знову ж в автоматичному режимі
Там же на складі є окремий цех, де на зимові шини встановлюють шипи
Крім безлюддя і майже стерильної чистоти виробництва вразила внутрішня система логістики російського «Нокіа Тайерс». Яку шину робити, по суті, визначають оператори. Спочатку це творці компонентів - вони бачать, що цех міксинг намешал потрібні склади гуми, замовляють її роботам-навантажувачів, завантажують і запускають потрібну програму. Далі точно так само роблять оператори складальних машин, отримавши дані про готовність компонентів. А перед вулканізацією шину «ведуть» взагалі тільки роботи, ні на секунду не втрачаючи з уваги жоден продукт, і самі визначають, в яку форму що залежить. Де який склад і які комплектуючі - це визначається по стікери, на яких закодована вся інформація про продукт. Але найперше завдання формується на підставі запиту відділу продажів: отримали замовлення від дилерів, сформували партію, комп'ютери перерахували на компоненти і склади - заважайте гуму. Як не дивно, плутанини від цього немає, перерахунок замовлення відразу в суміші замінює кілька десятків людей, і компанія економить на зарплаті. Але при цьому витрачається на навчання - кожен оператор повинен прослухати курс по комбат-планування, щоб, приступивши до роботи, орієнтуватися в системі.
Але головне враження від заводу в тому, що російське підприємство може бути цілком конкурентоспроможним на світовому рівні. А причиною тому холодний, як фінська зима, розрахунок, точне, як шип в шині, виконання і гордість за результат.